В своей повседневной жизни мы постоянно сталкиваемся с различными промышленными продуктами, но нечасто представляем, как и откуда появляются эти изделия. Попробуем рассмотреть в деталях процесс производства такой тривиальной вещи, как компьютерный корпус. Это не самый передовой компонент в современном компьютере, тем не менее, для его создания используются фактически все современные технологии. Чтоб не запутать читателя разобьем статью на несколько частей и постараемся максимально проиллюстрировать весь процесс. Условно можно разделить производство на следующие этапы:
- Работы по металлу
- Пластик
- Покраска
- Блоки питания
- Финальная сборка
Также стоит обратить внимание, что на большинстве производств имеется несколько сборочных линий, плюс в данной статье использованы фотографии с различных предприятий. Поэтому не удивляйтесь, если на различных этапах участвуют компоненты различных корпусов и БП, отобраны просто наиболее удобные кадры.
Металл
Именно он составляет основную массу и объем компьютерного корпуса. Большие компании могут позволить себе закупку проката прямо у металлургических компаний, мелкие – на различных металлобазах. Изначально компьютерный корпус выглядит примерно так:
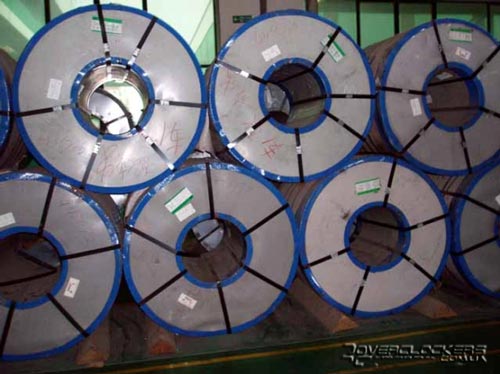
В рулонах прокат разной толщины, поскольку корпус обычно состоит из металла нескольких видов. Стенки и боковые крышки – самые толстые. Несущий каркас – чуть тоньше. Корзины для устройств и прочие элементы – из самого тонкого металла. Рулоны разматывают и режут на полосы нужной ширины.
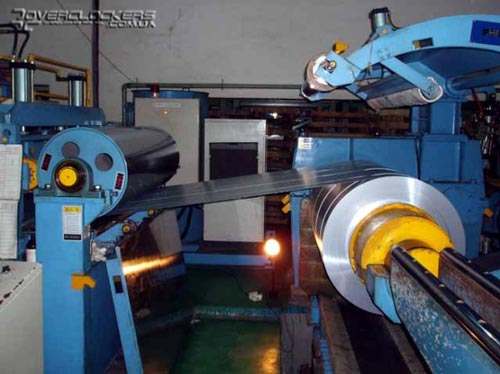
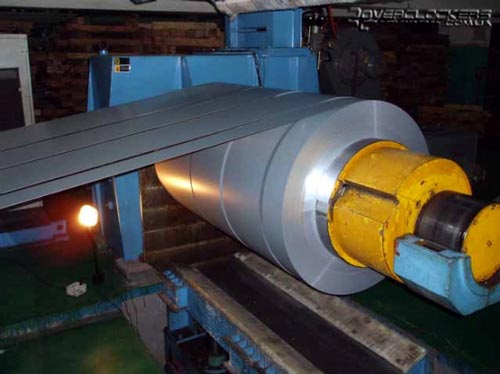
После этого следующий станок режет полученные полосы на куски нужного размера. Конечный продукт складывается в стопки и готов к дальнейшей обработке.
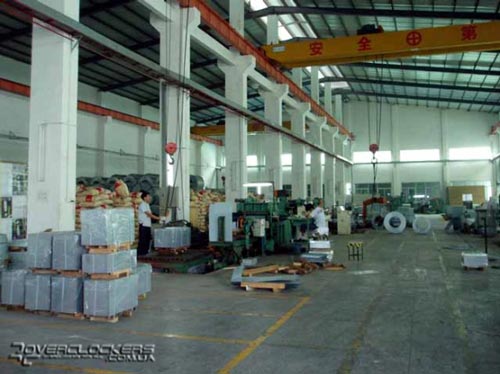
Полученные пластины поступают в цех штамповки. Перед описанием штамповки хотелось бы рассказать о так называемых "пресс-формах". Это те самые конструкции, между которыми сжимается металлическая пластина для придания ей нужной формы. Обычно каждый элемент проходит несколько прессов со своими пресс-формами, а для сборки корпуса требуются десятки различных элементов. В итоге на производство одного каркаса требуется 30-60 прессов и соответствующее количество пресс-форм. Их изготовлением обычно занимается специальный инструментальный цех. Каждая пресс-форма должна выдерживать нагрузку под миллион штампов в месяц в течение многих лет. Поэтому их производят из дорогой и твердой инструментальной стали. Обработка такой заготовки может легко длиться месяц-другой. Сначала инженеры моделируют форму и этапы обработки болванки. Потом последовательно на различных станках начинается работа над ней. Самые тонкие элементы выжигают специальной электрической дугой, позволяющей делать нестандартные и очень точные вырезы. Пару миллиметров металла такой аппарат может выжигать сутки. В конце пресс-форму дорабатывают и отшлифовывают вручную. Стоимость изготовления одной пресс-формы колеблется от 2-х до 20 тысяч долларов. И таких 50 штук на корпус.
Классический цех по изготовлению пресс-форм:
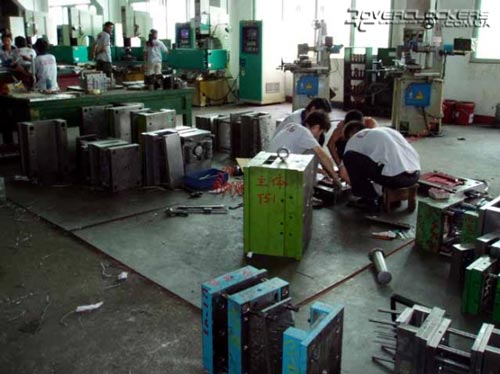
Так они выглядят:
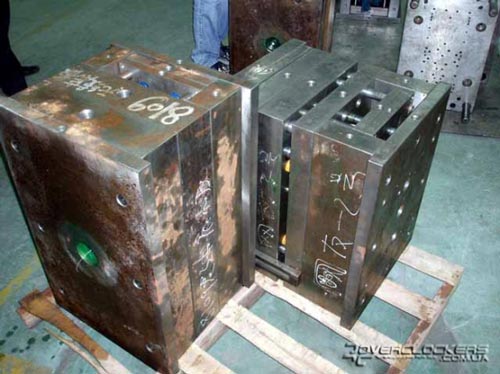
И так - хранятся:
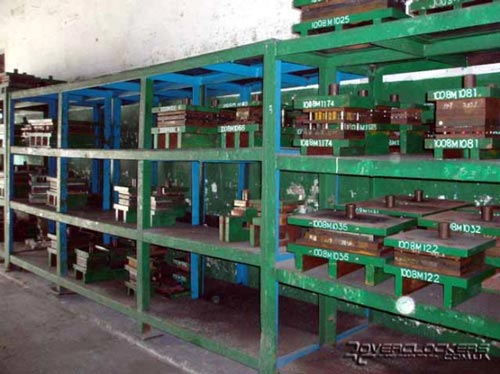
Примерно аналогично производится пресс-форма для пластика, однако там есть свои моменты в изготовлении. Для одной лицевой панели их нужно обычно до пяти штук, однако за счет сложности изготовления "закругленных" частей стоимость значительно выше. На фотографии – часть формы для литья корпуса мышки.
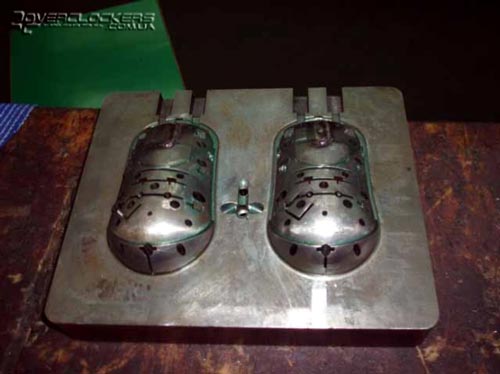
Итак, штамповочный цех. Тут работают сотни прессов, каждый из них выполняет свой небольшой кусочек работы. Заготовки поочередно передаются от пресса к прессу, постепенно приобретая законченный вид. Это самая шумная часть производства.
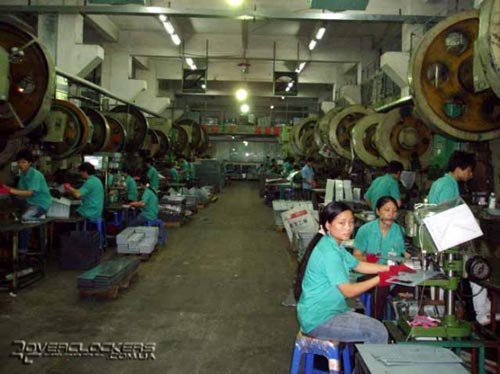
А этот станок за раз сверлит десяток-другой отверстий:
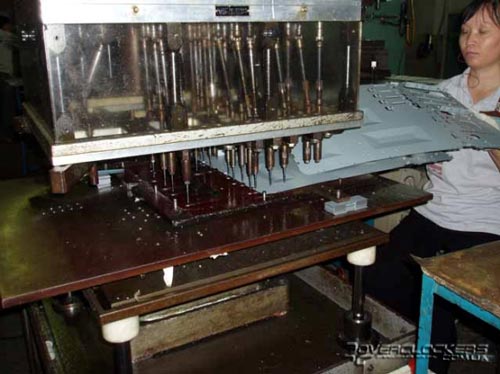
Все, металл готов. Он кладется на склад в ожидании сборки.
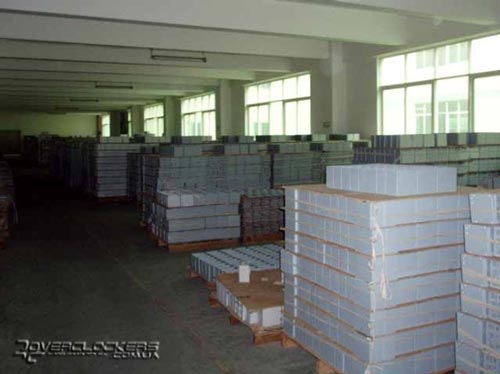
Пластик
Тут нас ожидает новый цех, состоящий из станков для литья. В аппарат устанавливается нужная пресс-форма. Далее в нее закачивают пластик. Потом он охлаждается и затвердевает, после чего форма раздвигается и вытаскивается готовая деталь. Китайский рабочий бодро обрезает все заусеницы и заряжает аппарат на следующее литье.
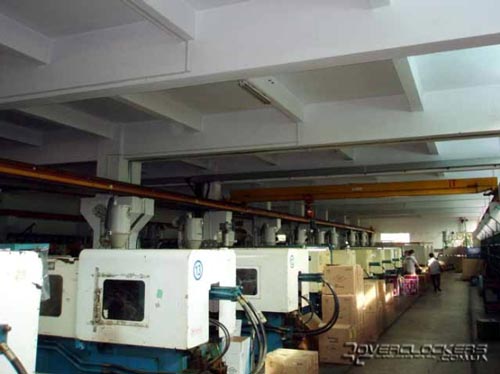
Обычно на каждом станке работают 2-3 человека.
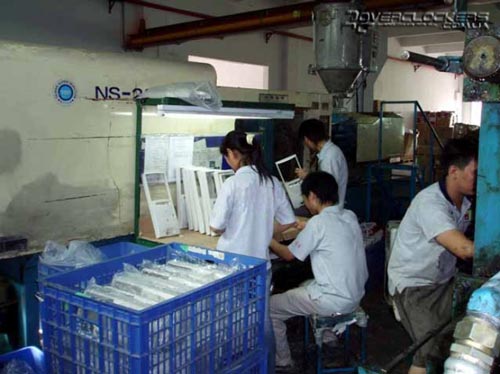
А тут льют корпуса для японских таксофонов – на фото пресс-форма в раздвинутом состоянии, лицевую панель только извлекли.
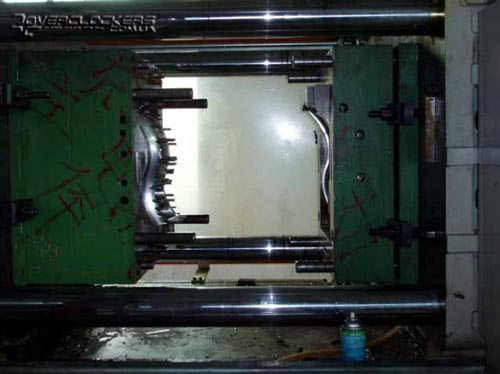
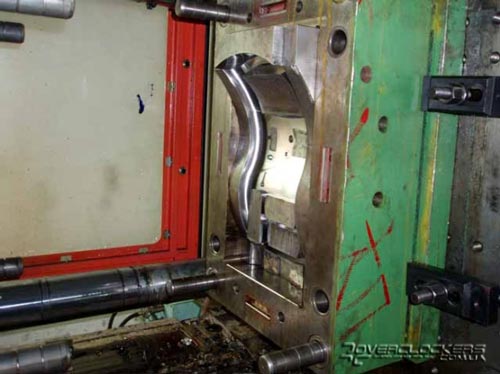
Покраска
Итак, металл и пластиковые детали готовы. Теперь предстоит их покрасить. Покраска – процесс творческий. Даже при наличии автоматической линии китайские Да Винчи и Малевичи после контроля качества докрашивают спорные моменты вручную. Собственно без покраски не обойтись – технологически и штамповка, и литье пластика сопровождаются небольшими огрехами. И только покраска делает поверхность идеальной, а точнее – однородной.
Ручная покраска пластика.
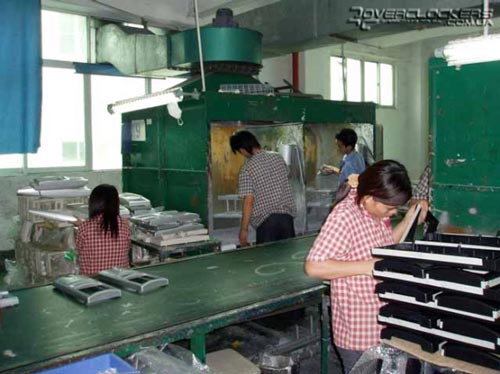
Далее детали поступают в сушильную камеру.
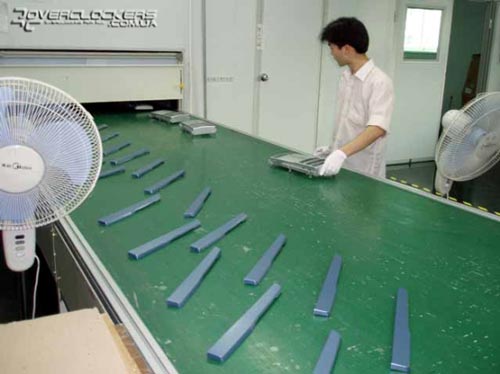
На выходе все элементы подвергаются бдительному досмотру. При малейших дефектах – на повторную покраску.
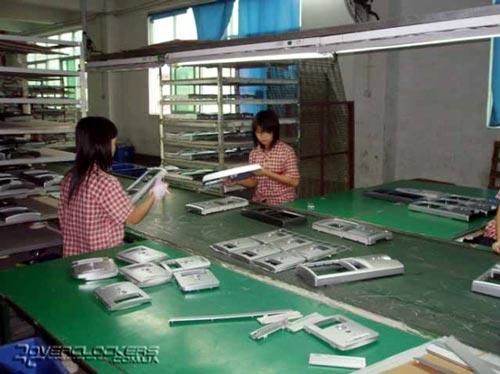
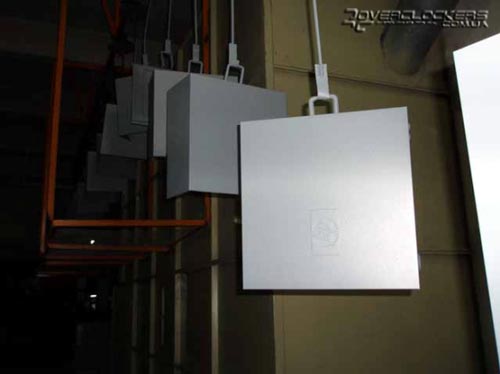
А это крышки корпусов HP после покраски.
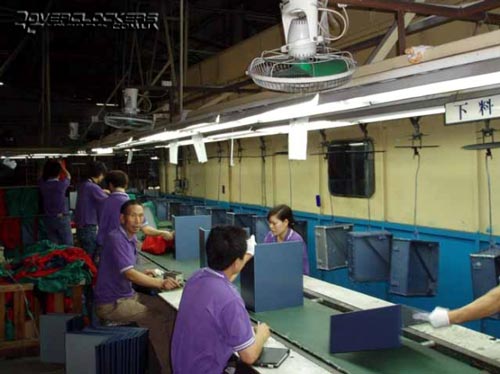
Их снимают со специальных "болванчиков", и опять же проверяют. Далее на все детали надеваются чехлы и отправляются в цех сборки. Но перед этим осталось узнать о том, как производятся блоки питания.
Блок питания
Опустим момент создания печатной платы, компонентов и собственно самой разработки блоков. Тут каждый старается как может – кто-то скопирует чужой блок, у кого-то целый отдел инженеров трудится над разработкой новых моделей. Самые продвинутые фабрики производят даже элементарную базу – мотают дроссели, льют разъемы. Некоторые закупают все комплектующие на стороне и производят только окончательную сборку блоков. Процесс производства БП везде примерно одинаковый. Печатная плата двигается по конвейеру, и каждый работник устанавливает свою группу элементов.
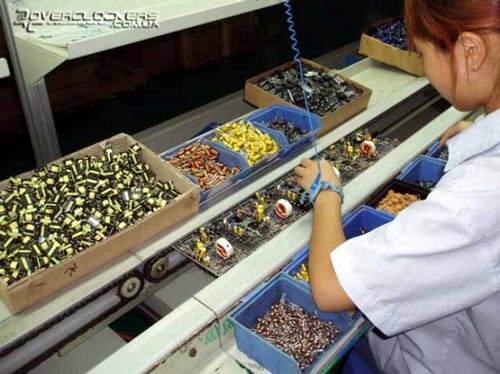
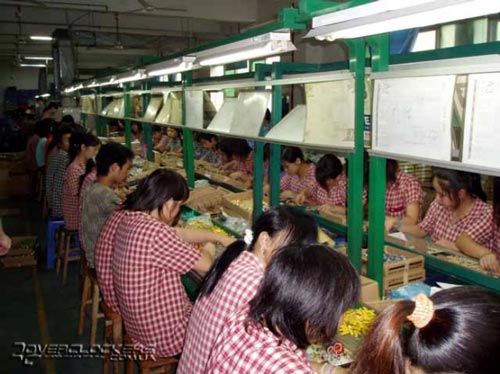
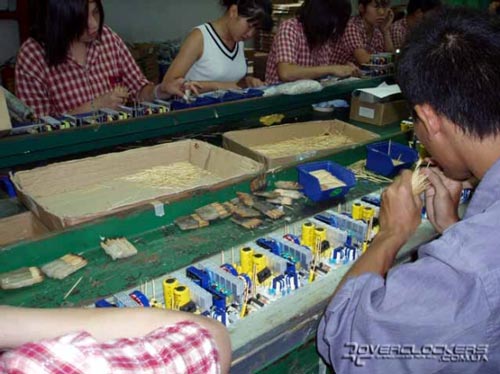
Пайка происходит чаще всего в несколько этапов, поэтому отверстия, которые нужны для следующей установки проводов или разъемов чаще всего заглушаются группами зубочисток. Это универсальное средство можно увидеть практически на всех фабриках, просьба владельцев "термалтейков" и "кулер-мастеров" не обольщаться и не надеяться, что их блоки собираются роботами в стерильных лабораториях.
Далее плата поступает на пайку. На сегодня существует классическая пайка оловом, а так же пайка по стандартам ROHS. Последний вариант отличается составом припоя и кондициями пайки. Многие фабрики, озабоченные поставками на европейский рынок, приобретают станки для пайки по ROHS. Оборудование новое, и все что на них произведено, соответственно на 5-10% дороже.
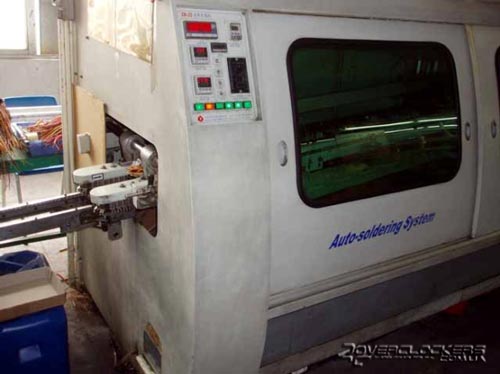
Это та самая "волна". Расплавленное олово стекает "водопадом", плата проезжает над ним и слегка касается нижней стороной. Простой и дешевый способ пайки, но, увы – не очень надежный.
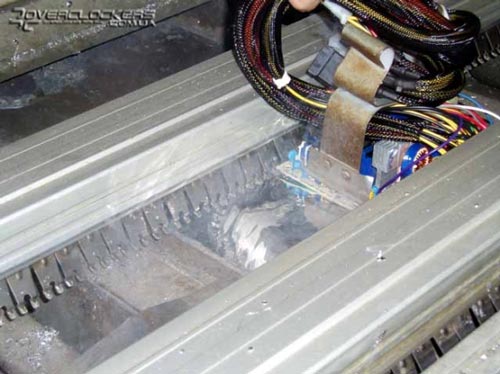
Китайский работник вынимает платы после пайки:
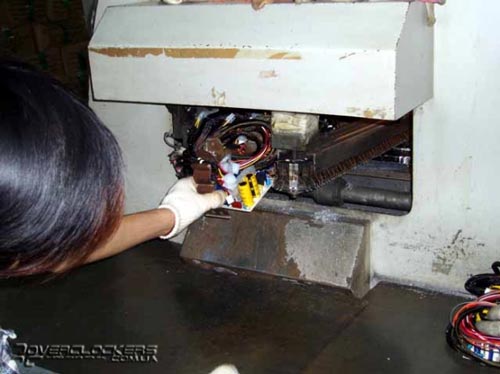
Следующая линия устраняет все неточности пайки. Каждый работник отвечает за свой участок платы. При надобности он допаивает нужные места вручную.

Настало время первого запуска. Плату подключают и убеждаются в ее работоспособности. Короткий тест на 10-15 секунд. Позволяет отсечь заведомо нерабочие платы.
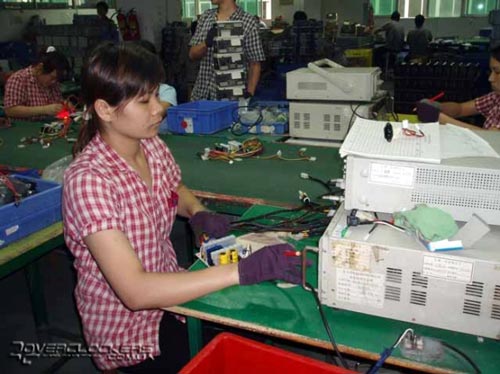
Работникам фабрик редко приходиться скучать. Время их расписано по часам и минутам. Обычно каждые два часа делается перерыв на 15 минут. В это время работник может выпить чай, сбегать в туалет или отдохнуть. Большинство предпочитает последнее. Рабочий, которого застал звонок на перерыв за переноской коробки, тут же роняет ее на пол и падает сверху, чтобы поспать.
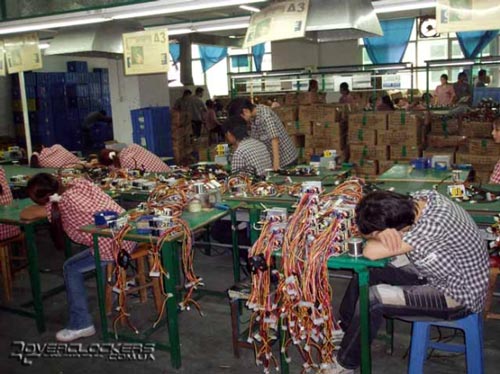
Прошедшую предварительное тестирование плату устанавливают в корпус и добавляют все необходимые разъемы, вентиляторы и прочие навесные компоненты. После сборки блок поступает на повторное тестирование. Оно так же не очень длительное – проверяется общая работоспособность блока, наличие "плохих контактов", проявляющихся при механическом воздействии.
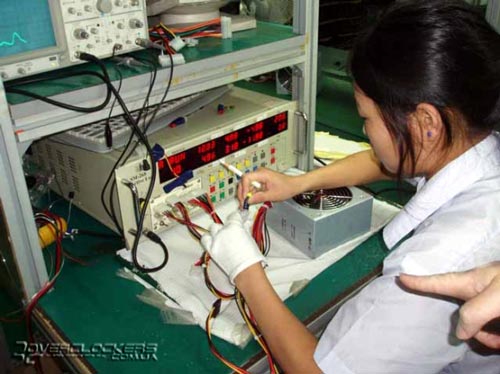
Блоки, прошедшие этот этап попадают на испытательный стенд. Каждый блок подключается к нагрузке, соответствующей примерно 80% номинальной. После этого блоки помещаются в термокамеру с температурой 40-45 градусов и тестируются 30-60 минут. Любой блок, не прошедший тестирование снимается и уходит на переборку.
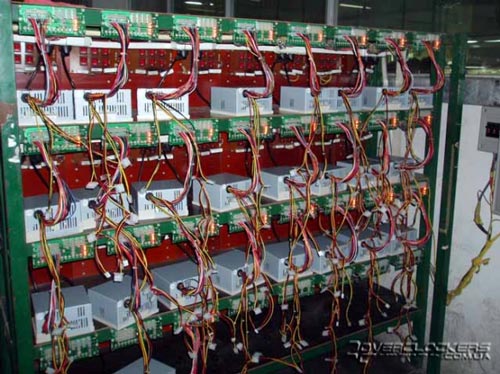
Прошедшие тестирование блоки проходят окончательный контроль. Их еще раз подвергают тестированию на удар, проверяют работу всех разъемов, а также более тщательно все выходные напряжения и защиты. После этого на блоки приклеиваются все этикетки и серийные номера, они упаковываются и готовы к дальнейшей продаже либо сборке.
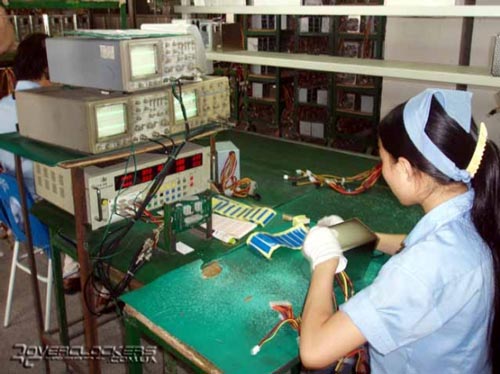
Окончательная сборка
Ах, как хотелось бы увидеть современную сборочную линию с длинными руками-манипуляторами, выполняющими монотонную работу быстро и качественно! Увы, роботы стоят дорого, а вот китайские рабочие – очень даже доступны. Абсолютно все этапы сборки корпуса производятся вручную. Для начала собирается каркас с помощью обычных заклепок – рабочие шустро орудуют пневмопистолетами.
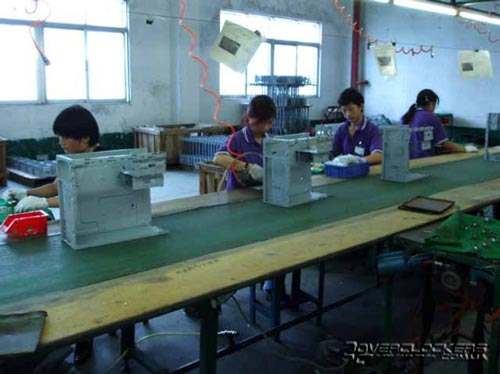
А это уже результат творческого полета китайской мысли – под столиком установлено сразу несколько пневмопистолетов, что позволяет устанавливать за раз 5-6 заклепок.
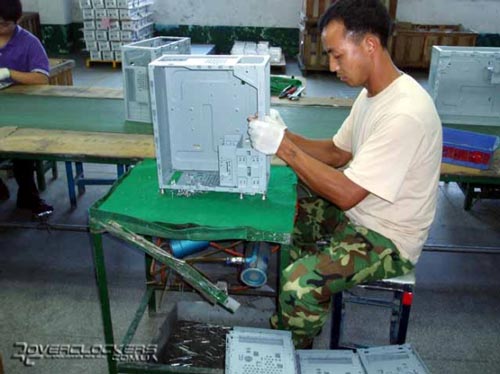
Корпус уже приобретает более-менее оформленный вид.
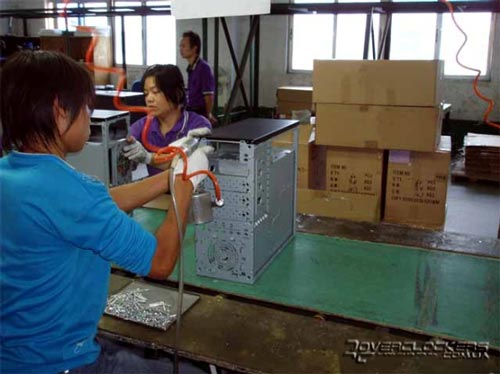
Далее добавляем блок питания, вентиляторы и прочее навесное оборудование.
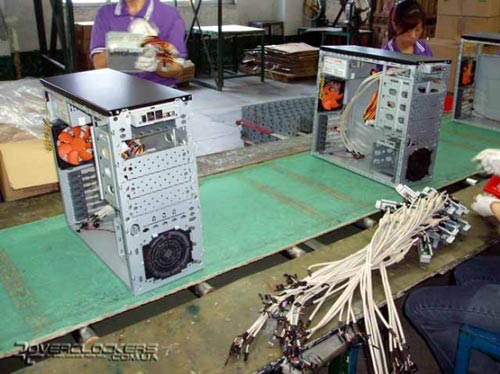
Теперь устанавливаем лицевую панель и добавляем набор крепежа с кабелем.
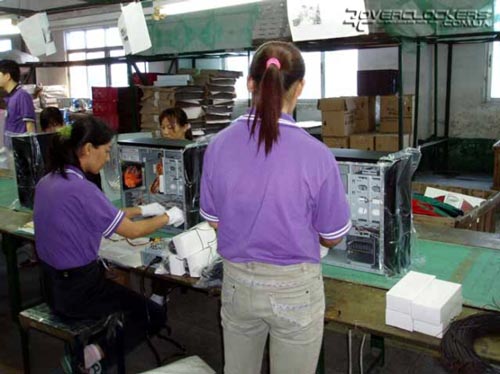
Корпус собран, упаковываем.
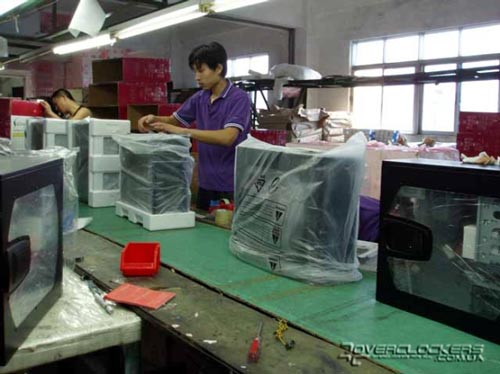
Вуаля – корпус для одного известного бренда готов и упакован.
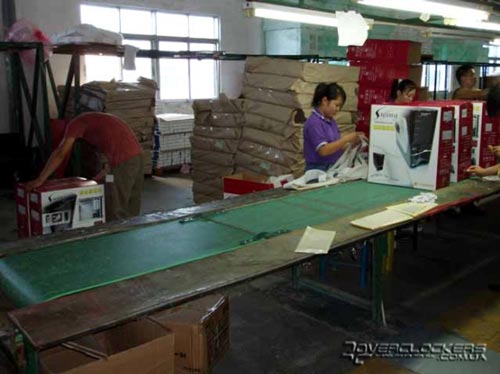
Теперь продукция попадает на склад и ждет тару, чтоб отправиться в любую точку планеты. Тут мирно уживаются самые разные бренды – Thermaltake и CoolerMaster, Gigabyte и HP.
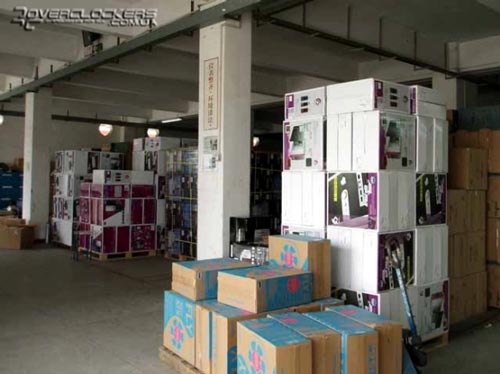