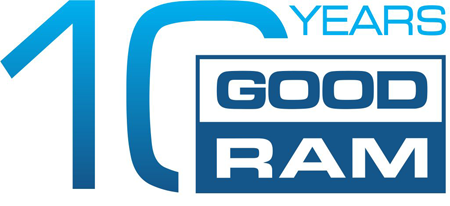
Прежде всего, немного вернемся в прошлое и познакомимся со становлением компании. Wilk Elektronik S.A. была основана в 1991 году и названа по фамилии основателя — Веслава Вильк (Wieslaw Wilk). Основной деятельностью тогда являлась дистрибуция оперативной памяти, а уже спустя несколько лет компания стала самым крупным дистрибьютором модулей ОЗУ на территории Польши. В результате успешной деятельности руководство пришло к решению открыть собственное производство.
Так, в 2003 году была открыта фабрика по производству оперативной памяти и создан бренд GoodRAM. Завод и офис компании с тех пор располагаются в небольшом городке Лазиска-Гурне с населением всего в 20 тыс. человек, расположенном неподалеку от города Катовице, центра угольной и металлургической промышленности Польши. По сей день подобное производство остается единственным на территории центрально-восточной Европы. Несколько лет спустя, компания также начинает производить и USB-флешки, а также разнообразные карты памяти. А еще немного позже во внимание производителя попадают и новомодные SSD. В этом году торговой марке GoodRAM исполняется уже 10 лет, что весьма немалый срок, учитывая особенность и территориальное расположение компании, ведь наверняка непросто конкурировать с азиатскими производителями, у которых необходимая инфраструктура находится на расстоянии вытянутой руки. Приглашаем наших читателей совершить виртуальную прогулку и познакомиться с основными этапами производства оперативной памяти на заводе GoodRAM.
Офис компании и производственный цех расположены в одном здании, площадью около 3000 кв. м.
Прежде чем попасть в производственный цех все сотрудники надевают специальные халаты и соответствующую обувь, защищающую от статического электричества, ведь, как известно, «статика» является одной из самых больших опасностей для микросхем ОЗУ. Кроме этого, при входе в цех имеется специальное устройство для проверки и сброса статического напряжения с тела человека.
Изготовление разработанных инженерами Wilk Elektronik печатных плат происходит у субподрядчиков компании и в производственных цех они попадают уже полностью готовыми для монтажа. На одной и той же производственной линии могут выпускаться любые типы продукции, начиная от оперативной памяти, заканчивая «флешками» и SSD, достаточно лишь разработать и инициализировать соответствующие программные решения для управления станками.
Платы, которые в будущем станут модулями оперативной памяти, именуются «мульти-блоками» и содержат сразу шесть планок ОЗУ.
Прежде всего, на плату наносится припой — для каждого типа плат предварительно изготавливается трафаретное сито, через которое паяльная паста продавливается на плату. Нанесение пасты производится специализированной машиной DEK Infinity, в которую печатные платы попадают из контейнеров, содержащих одновременно до 50 таких PCB.
Точность позиционирования «трафарета» перед нанесением пасты фиксируется высокоточными камерами относительно специальных направляющих точек, что обеспечивает возможную погрешность всего в 25 мкм.
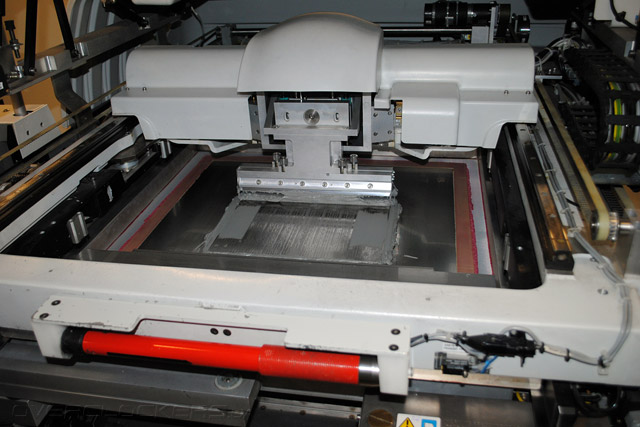
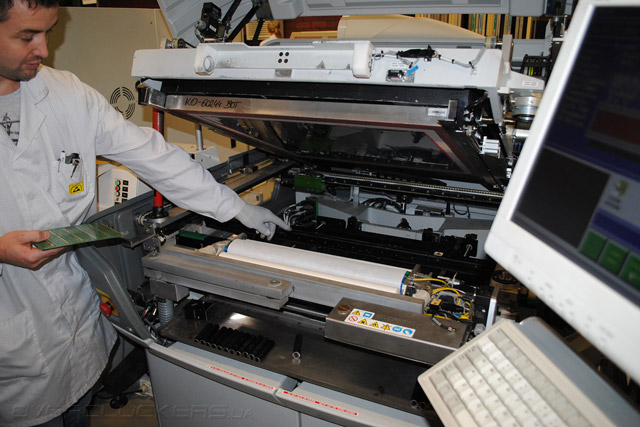
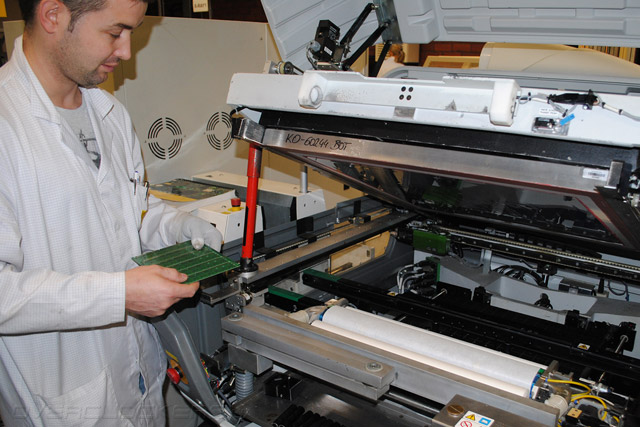
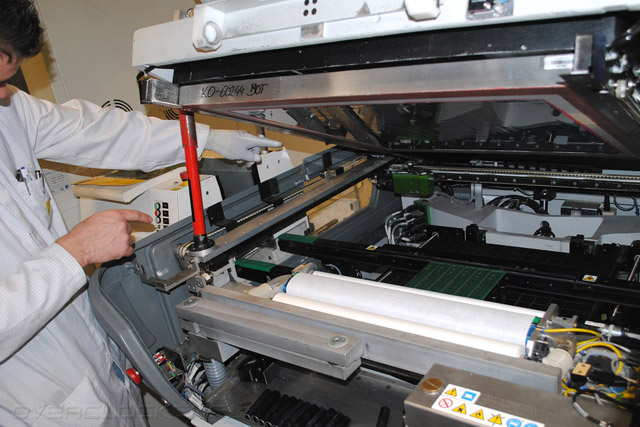
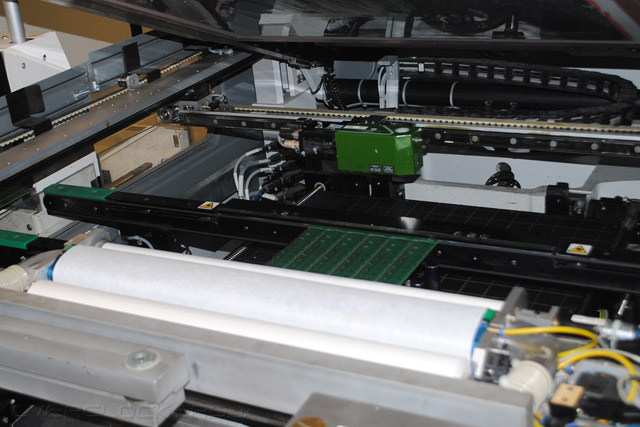
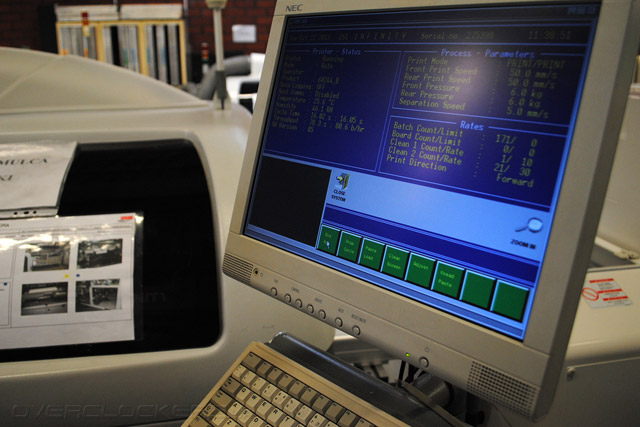
Циклично, через каждые 20 плат, сито автоматически чистится. Проверить качество нанесения паяльной пасты невооруженным глазом невозможно, поэтому для контроля используется микроскоп.

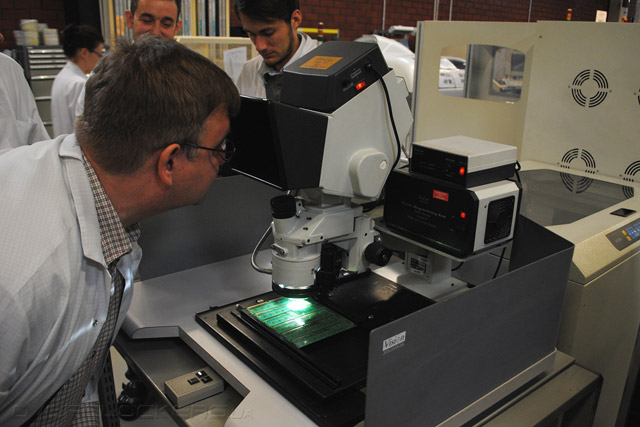
В машине для нанесения припоя поддерживается необходимая влажность и температура воздуха. Сама же процедура занимает считанные секунды.
Как только припой нанесен, платы по направляющим поступают в идущие следом по конвейеру машины, которые занимаются расстановкой элементов — чип-шутеры (chip shooter).
Буквально за несколько недель до посещения нами этого завода, компания приобрела новые станки для поверхностного SMT-монтажа Panasonic NPM-D2, обеспечивающие установку до 90 тыс. элементов в час — только вдумайтесь, это 25 элементов в секунду!
Отметим, что у старой производственной линии Fuji это значение было ограничено 42 000 элементами в час. Подобная модернизация оборудования компании обошлась в сумму около 1 млн. евро.
Итак, все электронные компоненты от производителей поступают в специальных лентах-катушках, чем-то похожих на бобины старых ленточных магнитофонов — так поставляются абсолютно все элементы: от пассивных до чипов RAM.
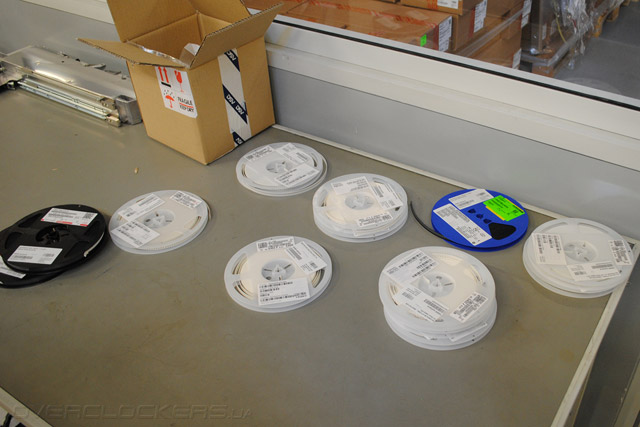
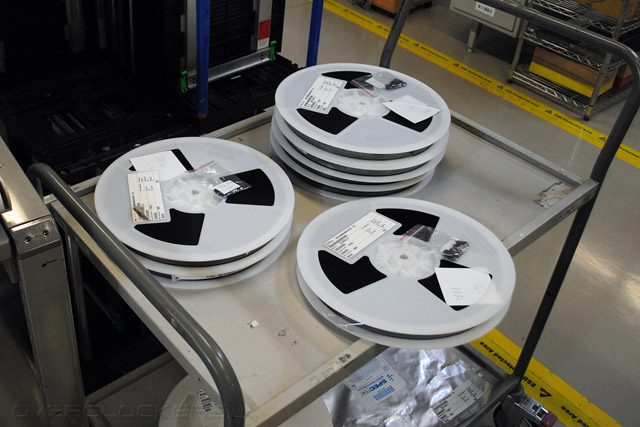
Ленты заряжаются в чип-шутеры и с впечатляющей скоростью машины Panasonic расставляют элементы на поверхности платы.
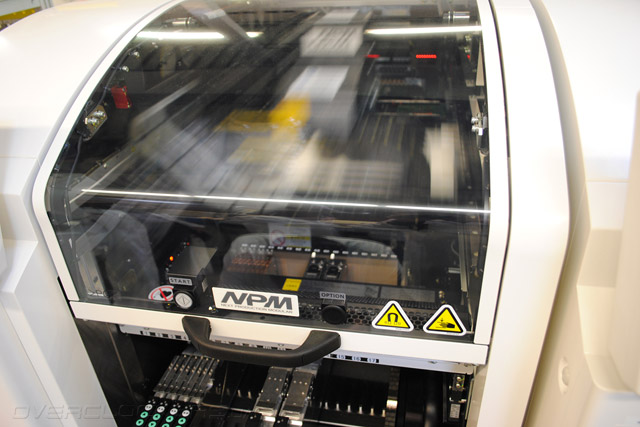
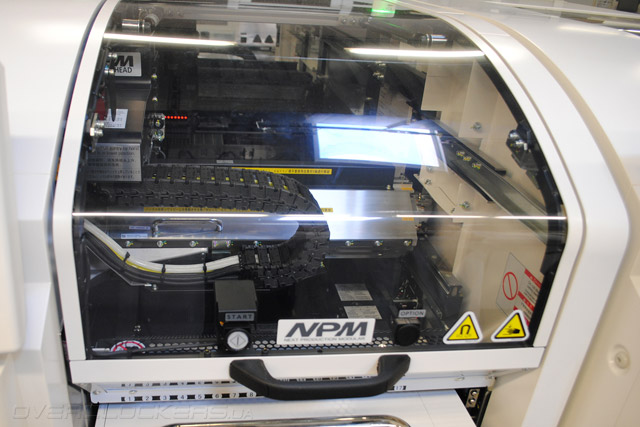
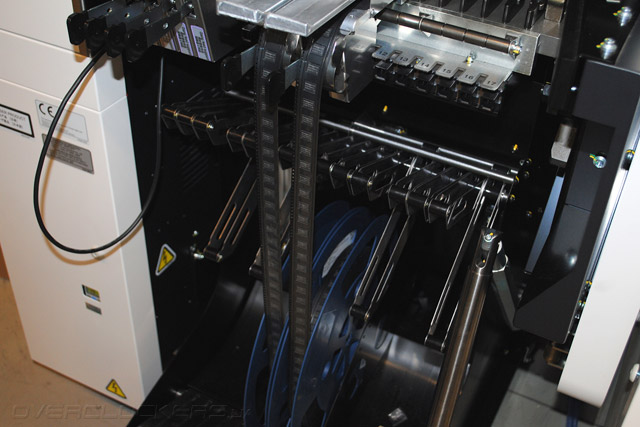
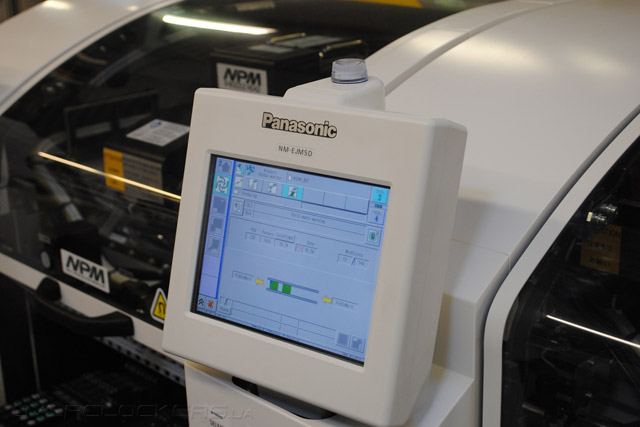
Пайка на данном этапе все еще не производится, элементы удерживаются на плате благодаря специальному клейкому составу нанесенной на предыдущем этапе пасты.
Вслед за этим проводится очередной визуальный контроль, при котором устраняются возможные неточности позиционирования, что, скорее, исключение из правил и такая процедура требуется крайне редко.
Далее готовая к пайке плата поступает в печь.
Ее камера имеет несколько температурных зон, температура в каждой из которых выставлена на определенном заданном уровне.
На начальном этапе температура возрастает — сначала происходит испарение составной части пасты, предназначенной для удерживания элементов на плате. Далее температура растет, плавится припой и элементы «прихватываются» к плате. На данном этапе значение температуры в печи достигает 235-250 градусов в зависимости от типа припоя и элементов. А уже в следующих нескольких сегментах печи температура последовательно понижается, обеспечивая окончательное затвердевание припоя.
После пайки платы загружаются в контейнеры.
При необходимости двустороннего монтажа, платы перемещаются в начало производственной линии и проходят аналогичный цикл еще раз, с той лишь разницей, что с учетом уже припаянных компонентов, «температурная кривая» в печи корректируется соответствующим образом.
Готовые платы проходят визуальный контроль качества пайки. Если производится монтаж BGA-элементов, где визуально нет возможности это проверить, так как контактные площадки скрыты под самими чипами, то для оценки качества используется рентген.
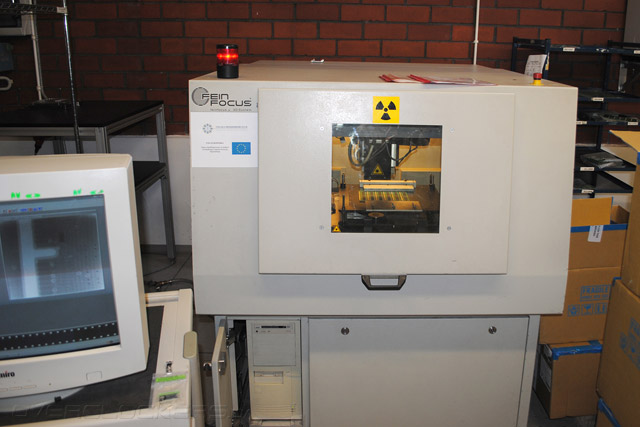
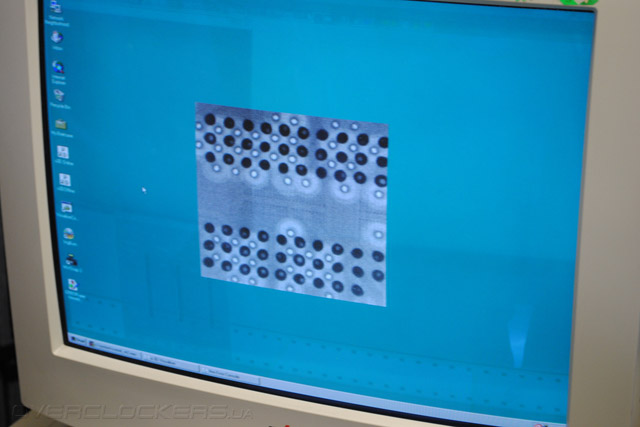
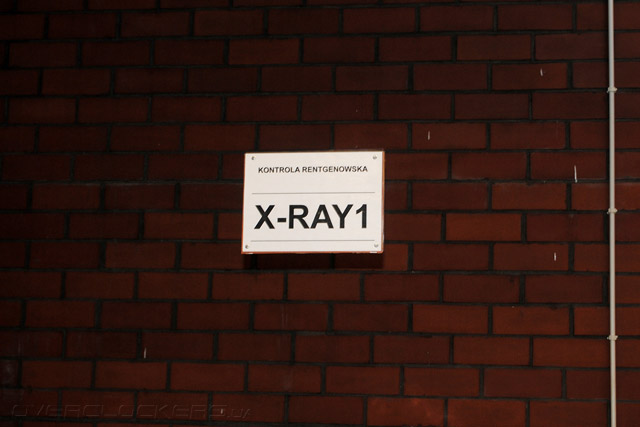
Если точки пайки однородны и выглядят темными — все в порядке. Если же имеются неровности, неоднородность заполнения припоем — это проявляется на рентгене в виде белых точек или пятен, такие платы отбраковываются. Уровень пайки не в последнюю очередь зависит от качества нанесения припоя и точности расстановки элементов. По словам инженеров цеха, увидеть представленную выше картинку, информирующую о некачественной пайке, при использовании подобного высококлассного оборудования практически невозможно.
В конце «мульти-блоки» разделяются на отдельные модули, после чего происходит программирование SPD каждой планки.
В зависимости от договоренностей с поставщиками чипов, микросхемы могут быть, как маркированы, так и не маркироваться. В последнем случае, при надобности может проводиться лазерная гравировка на специальном аппарате. Здесь же маркируются и флеш-накопители.
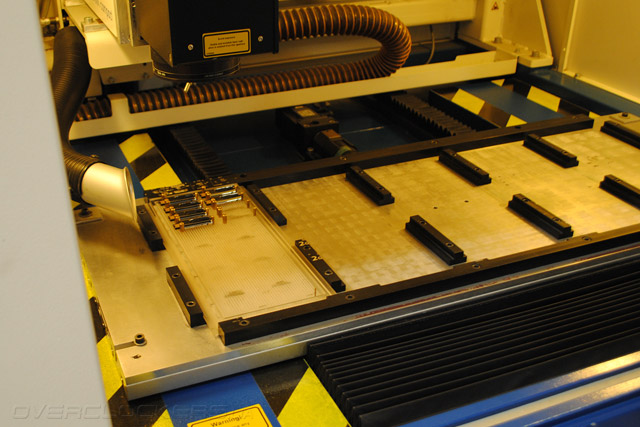
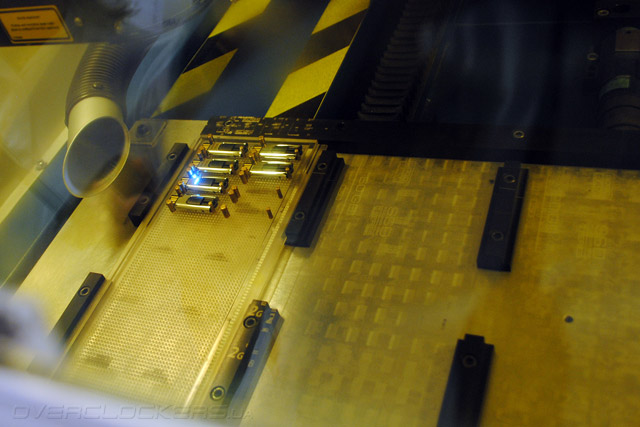
Разумеется, после завершения производства устройства попадают на тестирование. Несмотря на то, что существует специализированное оборудование для тестирования модулей ОЗУ, производитель выбрал более приближенную к реальности схему — тестирование на обычных системах, что и дешевле, и более практично в конечном итоге.
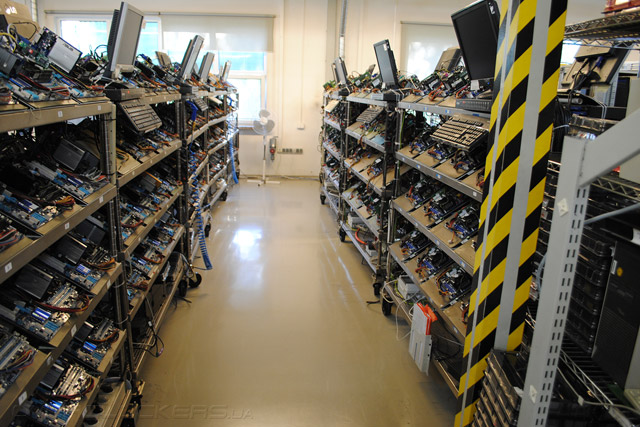
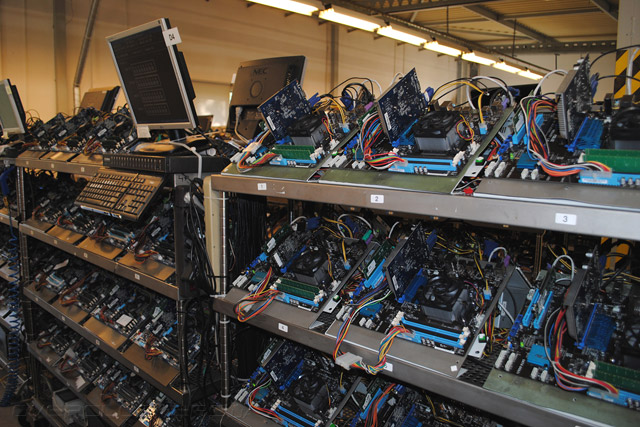

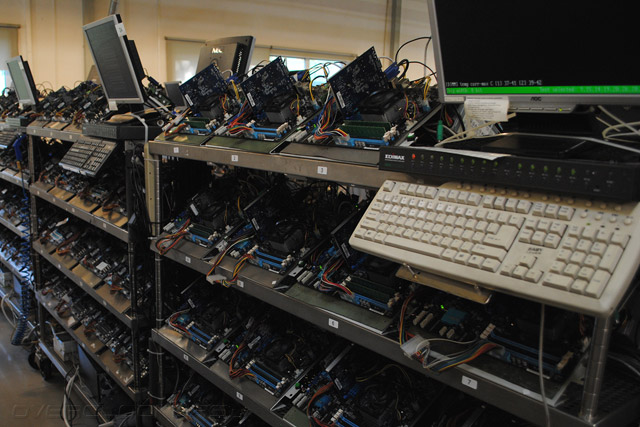
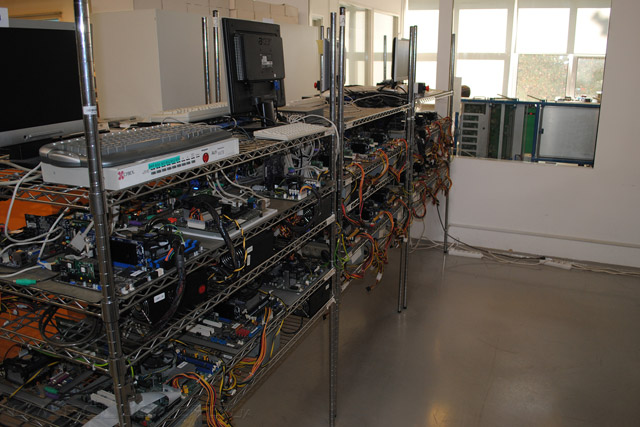
Несколько стеллажей содержат около трех сотен тестовых стендов, каждый из которых позволяет одновременно проводить тестирование пары модулей. Все тестовые системы связаны в сеть и контролируются с отдельной администраторской рабочей станции. Применяются как машины на процессорах Intel, так и на AMD. Из того, что удалось узреть, тестовые стенды строятся на базе плат ASUS, Gigabyte и MSI. В общем, процесс тестирования максимально приближен к практическому применению конечного продукта. На этом же этапе выясняется частотный потенциал модулей.
Завершающим этапом производства является упаковка продукции. Это происходит в соседнем с цехом помещении.
В ассортименте решений GoodRAM имеются модули памяти оверклокерских серий Play и Pro, которые перед упаковкой оснащаются пассивной системой охлаждения. Радиаторы поступают от изготовителя с уже нанесенными термопрокладками, защитное покрытие которых свидетельствует об их производителе — 3M. Процесс установки радиаторов происходит вручную, ловкости сотрудников можно позавидовать.
Wilk Elektronik уделяет большое внимание качеству упаковки своих продуктов. Следуя экологическим нормам, компания практически ушла от блистерной упаковки из пластика и теперь она состоит преимущественно из картона. Казалось бы, что может быть проще, однако, по словам представителей компании, дабы достигнуть нужного качества материалов, на этапе поиска производителей бумажной упаковки был сменен далеко не один такой поставщик.

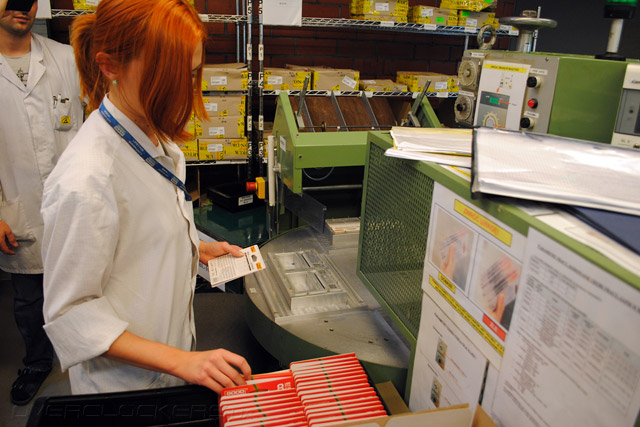
На производственных площадях присутствует еще одно крайне интересное помещение — оно полностью защищено от внешних воздействий, допуск в него жестко ограничен, и по словам, там даже не работают мобильные телефоны.
В этой комнате производится запись какой-либо информации на носители, в том числе и конфиденциальной, если, например, имеется подобно рода требование от заказчика.
Как уже упоминалось, описанная производственная линия используется для производства всех видов продукции компании — модулей памяти, флеш-накопителей и SSD-дисков. По словам инженеров, первоначальная подготовка и программирование линии для изготовления нового продукта может занять в общей сложности несколько дней. Однако перенастройка линии на уже известные алгоритмы занимает считанные минуты. Подобный подход позволяет производственным мощностям практически не простаивать.
Wilk Elektronik уникальна тем, что это, по сути, единственная компания, производящая компьютерную электронику в Европе. При этом ей удается успешно конкурировать с азиатскими производителями, что обеспечивается штатом высококлассных специалистов, современным оборудованием и правильно разработанной логистике технологического процесса.
В ближайшее время мы постараемся познакомить наших читателей с продукцией бренда GoodRAM, обратив внимание на оверклокерские серии модулей оперативной памяти Play и Pro, а также новую разработку компании — SSD-накопители C-Series, использующие контроллеры Phison.