Сейчас, когда серый ящик из разряда диковинок, а акриловое окно чуть ли не в каждом приличном корпусе, установкой пары вентиляторов или светодиодов никого не удивишь, тем более, используя заводские аксессуары. Моддинг давно повзраслел и творческие личности теперь выражают собственную индивидуальность путем кардинального изменения внешнего вида устройства или постройки корпуса с нуля. И если ранее моддеры только делали неуверенные шаги в этом направлении, то сейчас из под их дремеля выходят настоящие произведения компьютерного искусства. Практически каждое их творение привлекает множество людей, которые с неподдельным интересом следят за процессом работы, получая в конце эстетическое удовольствие.
Помимо различной тематики моддинг-проектов, будь то хай-тек, постапокалиптика, стимпанк и др., при поддержке компаний-производителей компьютерных комплектующих могут создаваться так называемые «рекламные моды», популяризующие ту или иную марку. Например, такие как робот MSI Defender, встречавшийся на различных выставках и поразивший своей уникальность, размерами и массой.
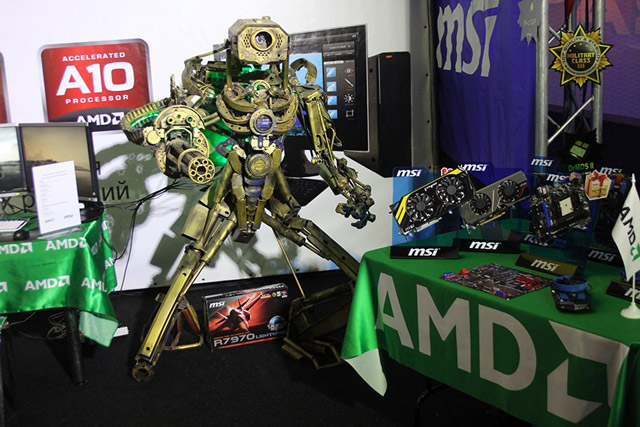
Этот кастом-кейс создавался всего два дня, а его автор был настолько суров, что даже не делал эскизов и черпал вдохновение из своей головы! К сожалению, процесс постройки так и не был запечатлен.
Но транспортировать такой талисман оказалось крайне тяжело, и в этом году при поддержке MSI было решено сделать небольшой, но не менее оригинальный проект — MSI Dragon. В качестве темы для будущего компьютерного корпуса выбрана серия игровых продуктов Gaming.

В этот раз процесс создания наконец-то будет описан и опубликован в виде ворклога на протяжении всего времени постройки, а это в течение ближайших двух-трех недель. Каждый этап мы запишем в виде отдельных страниц данного материала. Сам же кастом-кейс реализуется на базе студии «Моддинг-мастерская».
Этап 1. JUST START!
Сейчас ворклоги принято начинать с публикации рендера будущего корпуса. Мы привыкли действовать более традиционными, олдскульными методами. Перед началом работ сделаем макет корпуса из низкотехнологичного материала, такого как макетный картон. Материал толщиной 3 мм позволит создать макет корпуса в натуральную величину, что даст возможность провести примерку комплектующих ещё до фактического изготовления и тем самым свести к минимуму сложности в процессе реализации нашего проекта.
Итак, настало время макета. Мы распечатали изображения ключевых деталей «корпуса» в масштабе 1:1 на виниловой плёнке. Плёнку наклеили на макетный картон.
Теперь можно выпилить детали на стационарном лобзиковом станке. Высокая точность на данном этапе не требуется. Пилим «материнскую плату»:
Лапы и тело дракона выпиливаются по отдельности.
Потом к нам приехал комплект мощного «железа».
А после «железа» мы получили алюминий.
Качество — в деталях. Мы получили полкило высококачественных метизов.
Пока мы ждём доставки материалов для каркаса дракона и щита можно начинать работу над мечом.
Основой меча выступают два алюминиевых профиля квадратного сечения 25х25 мм и толщина стенок 1,5 мм. Профиля мы стянем вместе при помощи штифтов М4 длиной 8 мм и винтов с полукруглой головкой М4 длиной 8 мм (которые мы укоротим до 3 мм). Первым делом мы выравниваем заготовки и скрепляем вместе струбцинами.
Затем мы размечаем заготовку и керним отверстия.
Приступаем к сверлению заготовки.
Нам нужно просверлить один профиль насквозь, а у второго только одну стенку.
Чтобы скрепить надёжно — сверлить нужно много и точно.
Когда все отверстия просверлены, в них нарезается резьба М4х0,7.
Для отверстий по краям заготовки мы предусмотрели штифты. Центральные же отверстия займут винты М4х8, которые мы укоротим на 7 витков. Подрезку винтов удобно выполнять дремелем.
Основным БП в нашем кастом-корпусе выступит БП Seasonic, габариты которого немного не вписались в ожидаемые нами, он оказался чуть длиннее стандартных габаритов. В итоге мы вынуждены его разобрать и модифицировать, для того, чтобы поместить его в корпус без ущерба для дизайна последнего.
На следующем фото отлично видно, сколько места высвободится без использования нагнетающего вентилятора.
Щит будет красивым благодаря своим небольшим габаритам, а красота, как говорится, требует жертв.
Теперь осталось перейти к каркасу, но чертежи пока в процессе и вскоре будут закончены.
В продолжении ворклога следите за тем, как мы поместим БП, кучу проводов, HDD и прочие детали внутри «щита». И, конечно же, начнём строить каркас дракона и самого дракона. Оставайтесь с нами!
Этап 2. Акрил
Для дальнейшего продолжения проекта нужно закончить ещё несколько чертежей, по которым на лазерном станке мы вырежем акриловые детали.
Первым на очереди у нас чертёж каркаса дракона, боковые декоративные накладки и ряд мелких деталей.
Следующим мы вычертили щит. Он будет состоять из четырёх отдельных деталей.
Голова дракона и крылья, я думаю, хорошо узнаваемы, а ворох мелких деталей — это будущие позвонки для хвоста.
Голова у нас по плану должна быть объёмной. Но, выклеивать её из плоских частей мы не будем — так мы не получим желаемый результат и необходимую «лёгкость» конструкции. Поэтому мы выполним сложную гибку головы из цельного куска.
Погнуть акрил можно было и в печи, но удобнее и нагляднее это можно сделать при помощи термофена.
На следующих фото видно, что голова уже приобрела необходимую нам форму. Для наглядности роль глаз на фото выполняет полупрозрачная виниловая плёнка-витражка. Выглядит отлично — можно делать глаза!
Для изготовления глаза нам понадобится небольшой обрезок красного полупрозрачного акрила, на который при помощи маркера переносим контур глаза.
Моддинг не моддинг без одного инструмента. На «сцену» выходит дремель. По намеченному контуру мы проходим гравировальной насадкой, чтобы разметить нашу заготовку.
Далее последовательно, шаг за шагом стачиваем лишний материал вокруг размеченной ранее линии.
Все работы выполняются при помощи высокоточного инструмента Dremel 400 digital и прямых рук.
Деталь постепенно скругляем, придаём необходимую форму.
Когда заготовка обрела нужную форму, работа с дремелем заканчивается. Далее наступает самый кропотливый и долгий процесс — шлифовка и полировка. Для шлифовки последовательно используется наждачная бумага с номерами 320, 350, 400, 500, 600, 800, 1000, 1500, 2000. Шлифовка выполняется вручную.
После завершения шлифовки всё ещё заметны небольшие царапинки и общая «замыленность», их мы уберём полировкой. Она выполняется войлочным диском вручную с применением полировальной пасты.
После двух часов работы над глазом мы получаем качественную, уникальную деталь. На фото наглядно показан вид заготовки до и после.
Самое время заняться остальными деталями. Мы вырезали каркас дракона и детали щита. Материал изготовления — 3-мм черный акрил.
Приступаем к предварительной сборке щита. Нарезаем резьбу в отверстиях двух нижних листов акрила и соединяем их винтами М3х6.
Для наглядности мы чуть подсобрали щит. В специально заготовленное отверстие вставляем заготовку меча. В таком виде уже можно снимать мерки для изготовления боковин и других деталей.
Наступила очередь предварительной сборки каркаса дракона, каркас будет двойным — заготовки из 3-мм акрила, соединенные по две. Между заготовками — латунные стойки длиной 20 мм с внутренней резьбой М3.
Каркас получился достаточно жестким, чтобы выдержать вес комплектующих, и достаточно лёгким, что тоже немаловажно.
Раз мы уже подсобрали каркас, неплохо бы и голову прикрепить!
Пока мы собирали каркас, к нам наконец-то приехала оплёточка JDDtech. Красивая, и мы не сможем удержаться… Поэтому следующей части ворклога мы начнём оплетать провода. Ждите продолжения!
Этап 3. Проводка и оплётка
Итак, мы получили оплётку, черного и красного цветов, диаметром 3 и 10 мм. Сочные красивые цвета. Что может быть лучше классического сочетания красного и черного?!
В таком проекте нельзя упускать из виду даже такую незначительную деталь как SATA-шлейф. Оплетать мы будем красный кабель длиной 1 м. Оплетку, тем не менее, используем черную, а термоусадку по краям применим красного цвета.
В оплётку диаметром 10 мм шлейф вместе с разъёмами заходит идеально.
На следующем фото отлично видно, что после натягивания оплётка «сидит» очень плотно.
Практически все провода, идущие от блока питания к комплектующим, нам придётся удлинить. Все работы по снятию мерок и удлинению, а как следствие и оплетанию мы сможем произвести лишь после сборки каркаса. Поэтому мы переключили своё внимание на такую малозаметную, но весьма важную деталь как кабель питания. Да, для кастом-корпуса мы изготовим кастом-кабель! Нам понадобятся медные провода сечением 1 мм2.
Кабель питания будет подключаться к корпусу через хромированный трёхконтактный разъём, специально переделанный для использования его с переменным током.
Зачищаем и облуживаем все жилы.
Затем провода припаиваем к разъёму.
На выходе имеем следующее:
Теперь снова время оплётки проводов. Кастомный кабель питания будет выглядеть лучше, если каждую жилу оплетать отдельно.
Провод питания нашего куллера тоже нужно будет оплетать, значит пришло время разобрать его.
Провод мы оплетём, а тем временем радиатор будет перекрашен в яркий красный цвет.
Фото готового SATA-шлейфа и кабеля питания мы прибережем напоследок.
Дальше нас ждёт необычная покраска деталей, очередная возня с проводкой и сборка деталей из акрила. Следите за нашим отчетом!
Часть 4. Металл-солянка
Металл-солянка — блюдо моддерской кухни, суп на крутом стальном, алюминиевом и латунном бульоне с острыми приправами. Усаживайтесь поудобнее. Мы начинаем!
Готовим сегодня по чертежу.
Резать будем нержавеющую сталь 0,4 мм. Листы данного материала поставляются скрученными в рулон. Общие габариты листа 1х2 м. Внутренняя сторона листа в защитной плёнке.
Пробная порезка, отлаживаем режим работы установки.
Когда пробная порезка дала хороший результат — можно резать капусту нержавейку. Станок запущен. Резать до готовности.
Спустя четыре часа вылавливания мелких деталей под станком мы закончили.
Дизайн дракона включает в себя «хромовую» чешую. На этапе проектирования всем всё нравилось, ничто не предвещало беды. Когда порезали — стало ясно, что для таких мелких деталей придётся найти нетрадиционный способ крепления. Шутка ли — нас ждёт точный монтаж чешуйчатой мозаики из более чем 750 элементов… Решение пришло из области кулинарии микроэлектроники, пайки и ремонта — вакуумный пинцет — ВАМПИР! Остаток дня прошел в играх с пинцетом.
Одной из особенностей данного корпуса будет уникальная система запуска компьютера. Компьютер включится от прикосновения кольца к рукоятке меча. Изготовление рукоятки и гарды для меча немного притормозилось, пока мы ищем нужный материал, а вот кольцо я вам покажу!
В «Моддинг мастерской» отсутствует необходимое для литья оборудование, поэтому мы вынуждены были обратиться к литейщику Валере.
Валера, настало твоё время! Мы выбрали дизайн. И Валера не подвёл. Сделал отливку трёх моделей колец в кол-ве четырех экземпляров каждого.
Справа налево. Первое кольцо очень маленькое для мужской руки — ни на один из пальцев оно не налезло. Второе кольцо мне понравилось. И, несмотря на то, что внутри было много окалины, шло оно туго, я его одел на палец, но снять не смог, так и хожу с ним… Третье кольцо подошло идеально и даже снималось с пальца, на нём мы и остановились.
Обтачивать литники и снимать нагар весьма увлекательно, ведь в моддинге не каждый день приходится делать кольца!
Мелкие доработки производились дремелем.
На следующем этапе мы очистили кольца азотной и соляной кислотами, а затем искупали в спирте.
Самая классная и приятная работа — полировка колец на войлочном диске с пастой ГОИ. Именно на этом этапе металл начинает блестеть и показывать свой золотистый цвет.
Не всё то золото, что латунь!
Приступим к приготовлению деталей из алюминия. Сверлим отверстия в торце прутка.
В полученных отверстиях нарезаем резьбу М3. Примеряем стойки, выравниваем верхний щит относительно нижнего. После выравнивания верхнюю часть каждой стойки нужно подточить под углом, чтобы совместить её с плоскостью верхнего щита.
Закрепляем стойки винтами, это самый сложный этап, т.к. верхний щит стоит под углом. Винты притапливаем, чтобы сверху лег ещё один «блинчик».
Далее мы приступаем к изготовлению планки с разъёмом питания и тумблерами. Мы долго ломали голову, из чего можно сделать такую планку, ведь она должна быть надёжной, прочной и лёгкой. Решение пришло из неожиданного места. Некоторое время назад, один из поклонников творчества «Моддинг мастерской» привёз нам из Киева полсотни килограммов разнообразных металлических деталей для применения в моддинге. Нескольким из них посчастливилось поучаствовать в кастинге на роль планки. Выбран был алюминиевый П-образный профиль, толщина стенки которого составила 3 мм.
Размечаем необходимую высоту нашего профиля.
Наносим разметку на боковые части при помощи лекала.
Обычная «малярка» для такого сложного контура не годиться, поэтому мы применим виниловую контурную ленту.
Чтобы лучше видеть линию реза проклеим наш контур виниловой лентой ещё раз, но на расстоянии 1 мм от края первой ленты.
Деталь нужно уберечь от повреждений — это как раз работа для малярной ленты.
Пилим, пилим…
Через 3 часа пиления деталь обрела нужную форму.
Зажимаем в тиски и вышлифовываем кромку металла.
Примеряем по месту.
В детали нам нужно просверлить ряд отверстий. В частности для разъёма питания и тумблера. С установкой остальных переключателей пока повременим.
Примерка по месту установки.
В следующей части ворклога нас ждут самые интересные работы: покраска, сборка частей корпуса, завершение работ по кольцу. Оставайтесь с нами!
2013 год был воистину неудачным как само число 13… В процессе подготовки пятой части блога мы разбили, повредили или забраковали большую часть акриловых деталей. Некоторые перечерчивали и перерезали по 3 раза. Но, благодаря этому корпус стал только лучше, отсеялись слабые звенья. Хотя, мы и потеряли кучу времени на переделках.
Сроки горят, нужно спешить!
Подсобрали щит на свежеизготовленных стойках. Сняли мерки, доработали систему крепления П-образной планки с разъёмами. Добавили ей дно, за которое мы её надёжно закрепим.
Долгожданный этап — покраска. Пересчитываем детали и подписываем цвета. Красим в два основных цвета — черный матовый и насыщенный красный (RAL 3000).
Радиатор процессорного куллера получился особенно красивый.
И наступил процесс предварительной сборки щита.
Когда все стойки встали на места, самое время продолжить «мучать» БП Seasonic. Мы уберём его корпус и сделаем тем самым его ниже. Разбираем, отпаиваем от платы провода разъёма питания, которые в последствии заменим и выведем на заднюю панель.
Для БП вырезали из акрила подложку, на которую мы установим БП на дистанцирующих стойках.
Провода БП мы в дальнейшем будем вынуждены удлинить, чтобы можно было их протянуть через меч. И теперь, когда БП надёжно закреплён и никуда не убежит — начинаем «Донецкую резню кусачками-бокорезами». Перед откусыванием проводов все они были промаркированы стикерами, чтобы не путаться при сборке.
Начинаем рассаживать «пассажиров» по местам.
По месту установки куллера делаем воздуховод, который направит весь воздушный поток на БП. Пластины воздуховода также выполняют функцию поддержки верхней крышки щита.
Попутно убрали желтую этикетку с куллера и заменили её на наклейку из плёнки под черный шлифованный алюминий, а также удлинили провод питания куллера и оплели его. Красота!
БП будет изрядно нагреваться, поэтому решено было для пущей надёжности экранировать верхнюю часть щита алюминиевой пластиной, которая примет на себя тепло БП. Пластину выпиливаем из черного шлифованного алюминия толщиной 2 мм.
Примеряем по месту установки.
Нарезаем резьбу в крепёжных отверстиях.
Край пластины у нас серебристый, но его мы выкрасим в красный.
Наш щит должен стоять ровно и выглядеть величественно. Черненые ножки с концентрической шлифовкой будут в самый раз!
Для временной установки (и чтобы уберечь от повреждений) используем малярную ленту.
Когда основные вопросы по щиту улажены — можно ставить меч, но для начала его нужно сделать. Два алюминиевых профиля не очень похожи на меч, поэтому из МДФ выпиливаем две боковины. Деталь сложная, т.к. нам пришлось делать острый угол в 39,5 градусов.
Ах, да… чуть не забыл. В мече нужно пропустить полсотни проводов от блока питания. Нам понадобятся отверстия с обеих сторон меча.
Теперь будем крепить боковины. Для сцепления МДФ с алюминием мы вынуждены использовать единственный надёжный вариант крепления — эпоксидный клей, но тогда наш меч станет неразборным. Значит, все винты, скрепляющие меч, нужно намертво зафиксировать, чтобы они не раскручивались. Для этого отлично подойдёт неразъёмный анаэробный фиксатор резьбы.
Последняя примерка по месту и клеим!
После нанесения клея — «бинтуем» меч малярной лентой, т.к. струбцины на такой детали использовать затруднительно.
Когда клей затвердел — самое время подумать над креплением гарды меча. Зияющие отверстия в торце нам ни к чему. Закрываем их чёпиками.
В нижней части меча закрепляем крепёжные уголки, перед их установкой нижняя часть меча оклеивается виниловой плёнкой под шлифованный алюминий. Основная часть меча также будет в плёнке под шлифованный алюминий, но это будет позднее.
Выставляем меч по месту установки в щите.
Есть опасение, что акрил будет изгибаться под тяжестью меча и дракона. Для предотвращения такой ситуации мы изготовим и установим усиливающую пластину из шлифованного алюминия толщиной 2 мм.
Вроде бы неплохо получается, но чего-то не хватает… Ах, да, гарда!
Долго мы думали, как её сделать, перебрали кучу вариантов. Она должны быть лёгкой, прочной и не дорогой. И тут я вспомнил про одно из моих любимых ТВ-шоу «Виртуозы пилы» на канале Viasat Explorer. Было бы чертовски круто выпилить гарду бензопилой из массива красного дерева! А нет. У нас нет под рукой бензопилы и массива красного дерева тоже нет. Но в новогоднее время самая ходовая древесина — ель и сосна. Сосновые рейки сечением 40х25 мм будут в самый раз для нашей затеи. Отрезаем два сегмента равной длины и стягиваем их вместе винтами. Болгарка, хоть и не самый моддерский, но, наверное, самый эффектный инструмент. И шумит почти так же громко как бензопила :)
Процесс художественного пиления древесины болгаркой очень творческий, делать фото было некогда. Много пиления болгаркой, немного дремеля, шлифмашины и уже через час гарда была готова, а мастерская покрылась толстым слоем древесной пыли и опилок. В воздухе стоял запах палённого дерева. Наши соседи едва не вызвали пожарников :)
Ещё одна сложная задача стояла перед нами. Нужно изготовить рукоятку меча, да не простую. Рукоятка должна быть полой внутри, красивой снаружи, а ещё лёгкой и желательно эргономичной. Миска свежего оливье внесла ясность в наши мысли. Ручку не обязательно изготавливать, её можно подобрать из уже готовых заводских. Мало ли хороших на свете ручек!?
«Садовый инвентарь», «Садовый инвентарь» беспрерывно твердил голос в голове, и рука сама потянулась и схватила… грабельки! Да-да, садовые грабельки. Между собой мы называем ЭТО «вилкой».
Немного поднатужившись, мы отделили рукоятку, от «вилочки».
Однажды я сказал, что этот компьютер будет включаться от прикосновения кольца к рукоятке меча. Где же волшебное кольцо? Где моя прелесть? Кольцо (на самом деле их два, одно запасное) оснастили декоративным «камешком» черного цвета.
Теперь волшебное колечко будет включать ПК. Раз, два, три — ёлочка гори! Для наглядности кольцо включает не материнскую плату, а сегмент светодиодной ленты.
Работает безотказно, включать ПК теперь сможет лишь хозяин кольца.
Ну, вот, самое интересное вам показал. Хотя, показал, да не всё! В дизайне корпуса у нас есть три основных цвета: черный, красный и хром. Для полноты картины неплохо бы закончить начатое и всё-таки доделать кабель питания. Мы долго подбирали цепь для провода. Да-да, цепь! Нашли, наконец, красивую и с большими звеньями.
Провода мы заплетём в цепь. Перебрав кучу вариантов плетения, мы остановились на самом простом и самом красивом.
Каркас — самая сложная акриловая конструкция в этом корпусе. Её даже фотографировать сложно. Попробуем сделать предварительную сборку.
В нутрии каркаса пройдут специальные проушины для проводов, чтобы избежать беспорядка с проводами.
Каракас собираем на предварительно окрашенных латунных стойках.
Получился объёмный «бутерброд» из акрила.
Добавим к каркасу голову, чтобы завершить примерку.
Пора изготовить скобы для крепления каркаса к мечу. Для них возьмём уже знакомый вам П-образный алюминиевый профиль толщиной 3 мм.
По краям монтажных отверстий вклеиваем шайбы — скобы «лягут» на них.
Наконец дело дошло до хвоста. Позвонки для него были изготовлены уже давно, теперь настал их черёд быть в центре внимания, но это будет уже в следующей части нашего ворклога.
В последней, завершающей, части будут закончены все работы по щиту, мечу, оплётке и дракону. И, конечно же, вас ждёт финальная фотосессия. Не пропустите!
Первоначальный план по изготовлению корпуса предполагал около 14 дней работы, у нас получилось в разы больше. Чем дольше длилась работа тем больше идей для корпуса появлялось, и тем больше работы прибавлялось… Заяц хотел сделать быстрее, черепаха хотела сделать качественно.
Путь черепахи
Чтобы наше кольцо начало работать, его нужно снабдить магнитом. В кольце есть подходящая ложбинка, зачищаем и вклеиваем в неё магнит. Приклеивать будем на эпоксидный клей с несколькими каплями красной краски, за счёт которой нам не придётся мучатся с подкрашиванием магнита в труднодоступных местах.
После высыхания можно примерять.
Проведём тестовую сборку щита. Нам нужно примерять по месту планку-держатель для жалюзей на задней панели.
Когда нужные отверстия просверлены, все зазоры проверены — можно приступать к покраске. Красим при помощи новой, необычной спрей-краски. Это, по сути, — жидкая резина PlastiDip. С её помощью мы получим эффект кожи. А ещё она даёт грубую матовую поверхность, что нам и требуется. Данную деталь покрасим красным спреем. Нужный цвет мы получим через 3–5 слоёв.
Держатель жалюзей, поддон материнской платы и держатель видеокарты мы также красим жидкой резиной, но уже черного цвета.
Когда краска высохла, мы потихоньку начинаем собирать все внутренние детали щита в кучу. На заднюю панель с кнопками мы уже нанесли надписи, так что её тоже можно поставить.
На следующем фото видно, что кнопка Reset немножко не вписывается в дизайн, это мы исправим изменив её до неузнаваемости. Будет видно на финальных снимках.
Неплохо бы завершить все работы по мечу. Теперь, когда каркас дракона готов, мы можем разметить и просверлить последние четыре крепёжные отверстия. С внешней стороны зенкуем под потайную головку.
Меч, для придания ему финишного вида, необходимо обтянуть виниловой плёнкой под шлифованный алюминий черного цвета. Направление штриховки на мече — вертикальное.
А раз меч у нас готов, то можно приступать к многодневной возне с проводкой. Откушенные ранее провода мы удлиняем и загоняем в оплётку. Все провода соединяются пайкой. Цвет удлиняющих жил один — синий, но они все пронумерованы, так что путаницы с проводами не будет.
По окончании пайки мы получили два огромных пучка проводов, такое разделение требуется для того, чтобы они прошли через два квадратных профиля внутри меча. К проводке у нас добавится SATA-кабель и провода к материнской плате — POWER и RESET.
Готовим поддон к установке на каркас.
Крепления прикручены к каркасу, но ещё не покрашены.
Устанавливаем и закрепляем поддон материнской платы.
Собираем куллер Zalman после покраски.
Устанавливаем процессор и устанавливаем радиатор.
Оригинальная наклейка на вентиляторе не вписывалась в дизайн и мы её сняли. Куллер стал безымянным. Но, охладитель у нас получился просто отменно, красивый, красный, тихий. И мы не стали обижать компанию Zalman. Подошли к вопросу творчески и изготовили новую наклейку для вентилятора.
Устанавливаем куллер и любуемся. Красивый красный цвет. И охладитель и наклейка вписались в наш дизайн.
Железо смотрится величественно! То что нужно!
Начинаем пытаться просунуть провода через меч, но это задача непростая... Приматываем к пучку длинный провод и через него вытягиваем их наружу.
Накладка на щит у нас должна быть обтянута плёнкой под шлифованный алюминий. Что ж, работа с плёнкой — моё любимое занятие. Не будем откладывать это в долгий ящик и приступим! Отрежем плёнку с запасом, приложим и сверим размеры.
Край плёнки приклеиваем к столу и приглаживаем шпателем к детали.
По краям прогреваем феном, чтобы плёнка «легла».
Подрезаем острым хирургическим скальпелем. Сначала, грубо с запасом, чтобы убрать основной кусок материала, затем — точно по краю.
Когда панель обтянута, неплохо бы довести её до финишного вида, для этого нам потребуется установить светящиеся буквы, основа которых — красный акрил, а сверху — нержавеющая сталь. На акриловые буквы наклеиваем прозрачный двухсторонний скотч, он будет держать накладки из нержавейки. Металл перед установкой натираем до блеска, потом это сделать будет ещё сложнее.
В верхнюю часть щита нам нужно встроить подсветку, места катастрофически не хватает, на это у нас всего 3 мм толщины материала. Первоначально для этого проекта была заказана светолюминисцентная панель, но она показала слишком слабое свечение, вариантов кроме сверхярких светодиодных лент просто не осталось…
Снизу ленты крепятся на 1 мм прозрачный акрил, который мы спрятали под плёнкой.
Верхний щит первоначально мы планировали красить резиновым спреем, но, как оказалось, применить его вместе с накладками из нержавейки просто невозможно. Пришлось пойти по альтернативному пути и затянуть верхний щит красной виниловой плёнкой. Цвет получился даже ярче, чем планировался для резинового спрея, поэтому, чтобы добавить контраста, мы поместим на щит не хромированного дракона, а черного, кожаного. Для этого нам потребуется так же воспользоваться виниловой плёнкой, на этот раз под кожу рептилии. Обтянем детали дракона из нержавейки черной плёнкой и в таком виде разместим на щите. Сочетаться будет отменно! На оборотную часть дракона приклеиваем прозрачный двухсторонний скотч 3M.
Дракон получился красивый, кожаный, но полуглянцевый. Нам это не подходит, поэтому чуть позже мы покроем дракона в 1-2 слоя жидкой резиной, она собьёт глянец и придаст общий для всех черных деталей оттенок и добавит мелкой фактуры.
Следующим этапом станет склейка боковин. Вырезаем из 1 мм прозрачного акрила две боковины с запасами по габаритам, чтобы удобнее было крепить.
Выставляем по месту и приклеиваем цианокрилатным клеем в два этапа: сперва низ, потом верх. Такой метод оправдывает себя, т.к. успеть качественно нанести быстросохнущий клей сразу на верхний и нижний торцы щита чрезвычайно сложно. При склейке акрил гнётся по форме щита руками, подогрев не требуется.
Когда клей затвердел самое время подумать про лишний торчащий сверху щита материал. Нижнюю кромку мы выровняли вровень с щитом, а весь запас остался вверху и сбоку. Нас снова выручит дремель, аккуратно подрежем акрил по самой кромке щита. Меня очень радует, что акрил прозрачный и видно где пилить!
После подрезки акрил подравнивается по всем сторонам, где это требуется и зашлифовывается на чистовую.
Получилось весьма изящно!
Прозрачные боковины нам ни к чему. Их мы затянем в плёнку под шлифованный алюминий. Тут основная сложность заключается в том, что работать приходится на вертикальной боковине.
Сверху оставляем небольшой запас плёнки, а снизу подрезаем по краю щита.
Теперь можно подсобрать щит. Закрепим накладку с уже установленными хромовыми буквами. Эта накладка прижимает и прячет край плёнки и винты которыми прикручиваются стойки.
Панель крепим красными винтами с полукруглой головкой.
Получается красиво. Можем сделать ещё лучше — протестируем подсветку букв! Отличное торцевое свечение, то, что нужно!
Я долго думал, как закончить заднюю часть, при этом оставив доступ внутрь щита и не ухудшив циркуляцию воздуха. Жалюзи будет то, что нужно!
Подгоняем длину каждой пластины по месту. После предварительной сборки видно, что «пальто не то». В надежде улучшить внешний вид жалюзи, обтягиваем их с двух сторон виниловой плёнкой под шлифованный алюминий. Это не помогло… Сплошное черное пятно. Черное на черном…
Есть идея — красные боковины и черные торцы! Торцы акрила вышлифовываются в мат вручную. Боковины обтягиваем плёнкой того же цвета что и щит. Контур, в котором устанавливаются жалюзи, жирно подкрашиваем красным.
Вот теперь то, что нужно. Без сомнения.
Пришла очередь крыльев. На станке для гибки акрила, придаём крепёжному хвостовику нужный угол наклона.
Крылья обтягиваем плёнкой под кожу рептилии с двух сторон. Примеряем хромовые накладки. После предварительной примерки плёнка также красим резиновым спреем.
Супер! Теперь пришло время наших позвонков.
Наносим краску в 4–6 слоёв, чтобы получить неровную насыщенную фактуру.
Когда позвонки высохли можно вдевать в них резиновые уплотнители. Через них пройдут наши кабеля для питания видеокарты.
Готово!
Попутно закатываем в красную плёнку и ставим уплотнитель в тризубец-хвостовик нашего хвоста.
Голова дракона у нас также как и некоторые другие детали обтягивается виниловой плёнкой под кожу рептилии. Она должна быть особенной, она должна выделяться.
Форма головы дракона только кажется простой, сложные перегибы зубов и нижней челюсти тяжело даются даже опытному мастеру…
После обтяжки головы даём плёнке отстояться и остыть, а потом подрезаем по краю скальпелем.
После завершения работы с плёнкой голова была выкрашена «пластидипом» красным изнутри, черным — снаружи. Также задуваем им дракона который будет лежать на щите. В данном случае одновременное применение и плёнки и «пластидипа» — настоящее новшество в индустрии как моддинга так и автотюнинга, откуда к нам и пришел PlastiDip.
Когда краска высохла можно снять защитную бумагу с двухстороннего скотча и приклеить дракона на щит.
Впереди ещё осталось немного грязной работёнки. Гарду меча для придания ей изношенной фактуры мы покрыли эпоксидным клеем, а сейчас настало время шлифовки излишков клея.
Когда гарда зашлифована самое время продеть через неё нашу электронную составляющую «чуда» и зафиксировать всё в рукоятке. Простейшими датчиками, реагирующими на приближение магнитного кольца являются герконы. Для надёжности мы запараллелили в цепи сразу 2 шт. После установки герконов в нужном месте рукоятки мы «пакуем» рукоятку горячим клеем, для надёжности.
Закрепить круглый полый шар на ручке меча не простая задача, но мы нашли простое и надёжное решение. В рукоятку ввинчиваются два самореза, шар заливается горячим клеем. Пара примерок позволяет нам точно поместить шар над рукояткой, затем оставшееся пространство намертво «пакуется» горячим клеем.
Когда вся рукоятка меча в сборе — можно задуть ручку «пластидипом», это сделает поверхность рукоятки еще более грубой и изношенной на вид. На ручку меча с двух сторон клеим три заветные буквы MSI.
После PlastiDip вручную, кистью, подкрашиваем буквы. Ровный слой краски нам не требуется и накладывание краски на слой «пластидипа» даёт слегка неровную и видавшую виды надпись. Это же меч, а не глянцевый рекламный лайтбокс!
Всё отлично, но ручка должны быть не серой, а черной, да ещё и кожаной на вид. Моддинг-мастерская принципиально не работает с натуральной кожей, поэтому было решено найти ближайший аналог. Гибкая, тягучая, черная и похожая на кожу самовулканизирующаяся изоляционная лента подойдёт как нельзя лучше. После натягивания на ручку, она останется там навсегда и никуда не слезет.
Нам осталось изготовить лапы, которые решено было делать из медного прутка диаметром около 3 мм для пальцев и около 4 мм для самой «руки». Пальцы представляют собой равные сегменты по 40–45мм длиной, на одном из концов нарезается резьба. Ответная резьба будет в когтях. Резьбу мы также нарежем на конце прутка, который крепит лапу к дракону. Пальцы плотно приматываются медной проволокой к основному прутку и затем тщательно запаиваются паяльником. Перед пайкой на пальцы надеваем термоусадку, чтобы они не спаялись между собой.
Лапы мы закрепим при помощи небольших втулок с резьбой на обоих концах. На конце к которому крепим лапу будет резьба М4, а на внутреннем, которым крепимся к каркасу дракона — М3.
Подобные цилиндры мы нарезаем и для изготовления когтей. В них резьба М3 нужна только с одной стороны. Длина заготовки под коготь равна 20 мм.
Резьба в торце цилиндра нам также пригодиться для закрепления заготовки на держателе, так вытачивать когти шлифмашинкой будет весьма удобно. Хоть инструмент и массивный, но работа по шлифовке такой детали интуитивно понятна и выполняется без особых сложностей. Алюминий весьма податливый материал и хорошо обтачивается. Единственная сложность выточить дюжину одинаковых когтей.
После шлифовки машинкой мелкие дефекты вышлифовываются вручную, а затем коготь полируется пастой ГОИ.
На следующем фото наглядно видно три основных этапа изготовления: цилиндр с резьбой, выточенный коготь, отполированный коготь.
Мне хотелось, чтобы нижние лапы были похожи на настоящие лапы, и чтобы они не были похожи на верхние лапы. Так что, для придания им натуральности, нижние лапы оснащаются рудиментарным отростком-когтем. Для этого допаиваем к лапе кусочек медной жилы и обтачиваем до нужной формы.
Когда лапы были готовы, у мен наступил ступор. Их нужно выгнуть и разместить на местах по-разному, но выглядеть это должно натурально и естественно.
Я пробовал себя в роли дракона, который держит поддон материнской платы.
Пробовал понять, как удержать поддон тремя пальцами…
Для углублённого понимания проблемы мне пришлось убрать два пальца с каждой руки и только после этого всё стало ясно! Один коготь должен прошить материнскую плату насквозь, а два других обхватить её, так и сделаем!
Пока идея не улетучилась, мы быстренько отформовали лапы и занялись приданием им финишного внешнего вида. Грубую кожу лап со складками мы выполним из черной оплётки, к тому же будет хороший контраст с отполированными когтями. На верхних лапах, чтобы подчеркнуть изящную форму кожистых складок, мы подкрашиваем гребень складки красной краской. Так его будет лучше видно.
Ах да, вид медного рудиментарного когтя на нижних лапах никуда не годится, его нужно так же выкрасить в красный.
А на длинную часть нижних лапок мы задекорируем своеобразным кожистым наростом. Своеобразным «коленом». Для этого мы применим черную оплётку достаточно большого диаметра, которая сможет так растянуться.
Для завершения работы по лапам осталось только примерять их по месту. Все четыре лапы намеренно сделаны немного разными, чтобы было натуральнее. Две верхние будут «держать» материнскую плату, две нижние находятся ниже платы и как бы своим положением демонстрируют, что дракон только что оттолкнулся от щита и взлетел.
Впереди у нас сборка хвоста. Его основой нам послужит толстая медная жила около 4 мм в диаметре, на конце, который будет закреплён на каркасе, мы нарежем резьбу М4. Но нарезать резьбу на медной жиле сложно, она слабо сопротивляется кручению и пытается вращаться вместе с плашкой. Льём маслице и жила прекращает сопротивляться нарезке резьбы. Славненько!
Теперь протаскиваем через каркас дракона провода, которые мы предусмотрительно загнали в оплётку.
Когда возня с проводами завершена — можно прикрутить наш медный пруток, на который мы нанизываем позвонки.
В промежутках между позвонками на жилу натягиваем термоусадку черного цвета, она не только скроет медную жилу, но и зафиксирует позвонки, тем самым не даст им сдвинуться в кучу. С термоусадки предварительно были удалены все заводские надписи, внешне она не будет выделяться и мешать восприятию хвоста как чего-то натурального, природного.
Общее время сборки хвоста с учётом установки позвонков и протяжки проводов — 5 часов. Это обусловлено тем, что диаметр отверстия в позвонках равен диаметру жгута, который через него нужно пропустить. Мы пошли на это сознательно, т.к. хотели избежать осевого вращения позвонка на проводах. Ведь если после протяжки провода сядут плотно, то и хвост со временем не потеряет форму и вид.
Наш щит во время работы над хвостом защищает винтажное полотенце олимпийским мишкой 1980 года.
Из хромовых деталей у нас остался центральный шип, который будет стоять за головой дракона и сотни чешуек. Сперва, разберёмся с шипом. Он представляет собой две симметричные хромовые пластины, между которыми зажимается черный 3 мм акриловый шип с шлифованной в мат кромкой.
Фух, закончили! Хотя, такое чувство, что я что-то упускаю… Что-то мелкое. Мелкое как чешуйки.
Сборка орнамента из хромовых чешуек — самая сложная и трудоёмкая часть работы над корпусом. Но они придадут ему именно тот финальный внешний вид, зрелищность и нужный уровень детализации.
Черепаха, которая живёт во мне, оттягивала день установки чешуек до последнего, поэтому сборка чешуек происходила ночью. Стол, на котором мы будем работать, был очищен от всяческого мусора, с него также был демонтирован сверлильный станок, а столешница была застелена хлопчатобумажной простынёй. Не очень фотогенично, зато предотвратит порчу чешуек. Большинство чешуек после лазерной резки хранились в отдельных пакетах, так что мы высыпали их на стол и стали сортировать и полировать. Сортировка заключалась в отделении правых чешуек от левых. Когда я продумывал дизайн, мне хотелось, чтобы чешуя с одной стороны была зеркальным отражением другой стороны, именно так и получилось, что чешуя у нас двух видов… Перевернуть левую и сделать из неё правую нельзя, т.к. при изготовлении плёнкой была защищена от царапин только одна сторона.
К каждой чешуйке мы приклеиваем кусочек прозрачного двухстороннего скотча 3М. Скотч на силиконовой основе, держит очень-очень крепко, оторвать чешую чрезвычайно сложно. Толщина скотча составляет 0,5 мм, что придаст узору дополнительный объём. Чешуя, немного удалённая от поверхности, выглядит более естественно. Чешуйки ставим вакуумным пинцетом по специальному акриловому шаблону. Зазор между чешуйками получаем равный 2 мм и одинаковый на всей площади узора. Заполняя накладку на каркас дракона чешуёй, мы оставляем неприкрытыми технологические отверстия для крепежа лап, крыльев и отверстия для крепления самих накладок к каркасу.
Процесс установки чешуек выглядел так: выбираем нужную чешуйку, снимаем плёнку, полируем, клеим скотч, хватаем вакуумным пинцетом, снимаем защитную плёнку со скотча и клеим.
Большой запас при изготовлении чешуи оправдал себя, в брак, по тем или иным причинам, у нас пошла каждая третья чешуйка.
После наклеивания чешуек они были наполированы вручную микрофиброй.
На установку чешуек на одну боковую накладку мы затратили более шести часов.
После тяжелой ночи в обнимку с чешуйками мы зевнули и поехали… Нет не по домам. В фотостудию. Где нас любезно терпели на протяжении пяти часов.
Наша работа над корпусом подошла к своему логическому завершению. Хотелось бы поблагодарить компанию MSI за доверие, терпение и за то, что этот корпус доверили именно нам.
В рамках работы над корпусом был использован ряд новаторских решений которые найдут своё применение в других модах. Первым быть не легко. Надеюсь, что наш корпус кого-то вдохновит начать свой моддинг-проект, кого-то закончить начатый.
Ранее мне не доводилось проектировать корпуса задевающие тематику животного мира, рождение данного корпуса сродни появлению первенца, сложно, долго, больно, но в итоге я доволен результатом. Сложность и детализация сводили нас с ума в процессе. Теперь, когда проект подошел к концу, могу сказать — это было круто!
Наши основные цели достигнуты — корпус имеет сравнительно малую массу. Со всей электронной начинкой и кабелем питания она не превышает 12 кг, дизайн корпуса отлично подчёркивает стилистику MSI Gaming Series.
Надеюсь, что читатели останутся довольны 6 частью нашего воистину эпического проекта.
Всем спасибо за внимание, за просмотры, за клики. Удачных Вам модов. \In MOD we trust/